建厂12年,产量从最初36万吨跃升到现在的163万吨。在过去的几年里,长庆油田采油十一厂生产成本递减,用工量递减,产量稳中有升……种种发生在采油一线的变化,都是得益于该厂率先探索试行智能油田建设开发新模式。
如今,一个高科技赋能的智能化绿色采油厂在陇东油区惊艳亮相,3653余口油水井、61座站场实现无人值守,在“一朵云、一个湖、多功能平台,支持多维通用应用”的高科技助攻下,采油十一厂成功试水黄土塬上集约、绿色标准化地面建设模式。将地面一体化智能集成装置、远程启停、语音报警装置、数字化监测等新技术陆续应用在油田管理中,实现了全过程在线监控,建立新型劳动组织架构,生产运行业务实行全流程闭环管理……生产、组织、管理实现全面升级,做到了省心省时、省人省事、省力省钱。
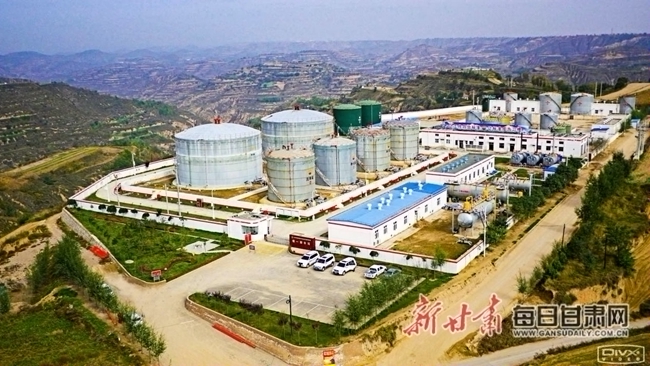
“智能生产”提高核心竞争力
伴随2014年以来油价大幅下跌,国内石油行业市场化体系不健全、竞争力不足等体制性问题凸显,管理水平较国际一流企业存在较大差距,行业可持续发展存在制约。采油十一厂在快速发展的同时,也面临着较多考验,如何精准处理原油产量的不断攀升与人力资源紧缺的矛盾,杜绝生产开发带来的环保隐患,在管理部门之间更为高效的信息沟通,及时解决油田生产技术难题成为亟待解决的问题。在大数据、云计算、人工智能等信息化技术的不断发展及深入应用下,这些问题迎刃而解。
立足鄂尔多斯盆地油气开发实际情况,长庆油田第十一采油厂充分运用物联网、大数据、云计算、人工智能等新技术,构建科研、运营、监督等支撑体系,筑牢统一数据湖、统一云平台两大基础,为场站无人值守、油气井智能生产、风险作业可视化监控、四维油藏模型、智能装备应用、人财物精准管理等业务领域提供全程应用支撑,探索出了由传统油气田企业向数字化转型、智能化发展的新路子。
采油十一厂数字化建设起步于2010年,目前为止,该厂仍在持续推进数字化建设,现已配套建成数字化场站94座,井场1168座,光缆4727公里,在5个作业区配套安装管线泄漏报警系统52套、穿跨越视频42套,截断阀22套,电动截断阀33套,浮油监测系统3套等数字化基础建设。该厂积极转变观念,精细顶层设计,狠抓责任归位,通过建设中心站和无人值守站,革新生产组织方式,推动生产组织架构优化,强化中心站职能,实现生产要素集约化、生产管理精细化、队站管理自主化、设备设施自动化,降低场站员工劳动强度,助推人力资源盘活,有效缓解用工紧张的压力。
“以前监控岗24小时在岗,工作时间全程神经紧绷,现在终于正常倒班,让我们感受到人性化的同时,生产效率也提高了。”采油十一厂新集作业区员工杨伟说。未实现无人值守建设前,新集作业区镇三联岗位员工每天要花费12小时进行数据巡察、站内巡检等工作。如今,全厂实现17座中心站、59座无人值守站建设,无人值守覆盖率90%,其中太白梁和新集作业区无人值守覆盖率100%。以此为基础,该厂合并全厂13座中心站和3座区级调控中心,形成作业区直管井站的“大监控、大调度”格局,压缩管理单元,实现集中监控+区域巡护的井站运行模式。截至目前,数字化采油作业区占比达到2/3,盘活岗位用工55人,作业区调控中心由“三班两倒变为四班三倒/五班三倒”,监控岗不再24小时上班,监控职责更能有效落实,员工幸福感攀升。这是继无人值守站减员增效后,扁平化管理再升级的又一大突破。
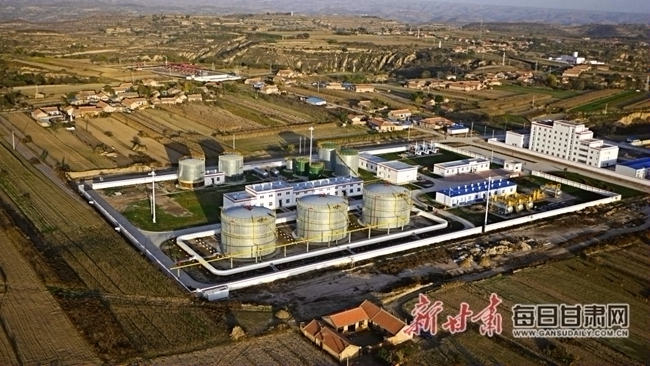
“智能管理”激活精准高效动能
按照“优化管理流程、规范基础操作”原则,采油十一厂智能化油田管理充分结合运行现状,坚持“让制度活起来,让规范融进去”的思路,探索研发智能两册管理系统。通过在新集、桐川作业区部署28套手持终端、214张射频卡、170张巡检卡,搭建据驾驶舱,实现作业标准化,辅助生产决策。为实现异常油水井工况智能诊断,开发部署智能油水井诊断系统7大模块28项功能34种诊断模型48项应对措施,形成单井病历、诊断结果及建议推送、措施跟踪及完井评价的闭环管理,已成为全厂科研人员日常工作平台。
针对智能化采油厂设计方案中所涉及的应用场景,采油十一厂突出“技术+管理”,优选2个作业区,8个井场,34口单井部署动液面测试仪、油井含水分析仪以及自动加药装置,并开展智能RTU、智能视频分析、上下游场站联动、机器人智能巡检等8项智能先导试验,分析现场监控画面3万余张,采集数据点680余个,形成分析结果16万余条,逐步探索出一套在“井场微闭环、站点小闭环、保障中闭环、厂级大闭环”四环围墙下的“厂级调控中心直管生产现场”智能采油厂管理架构。预计全厂运行效率提升20%。
采油十一厂在所辖桐川、新集等4个作业区输油管道上配套建设管道泄漏定位报警系统51套,在管道穿跨越两端安装远程截断阀26套。针对原油泄漏及时报警、定位,提醒当班员工,停泵停输,远程关闭截断阀,避免造成较大环境污染事故;在河流上游安装浮油监测装置,实时监测河流水质,出现异常情况时,及时报警。对注水泵、输油泵、抽油机等主要能耗设备安装智能电度表,通过前端监测点的电量在线采集,实时监测对比电能消耗,及时调整负荷及运行方案参数,达到节能降耗的目的。实现油田能耗“看得见、说得清、控得住”。
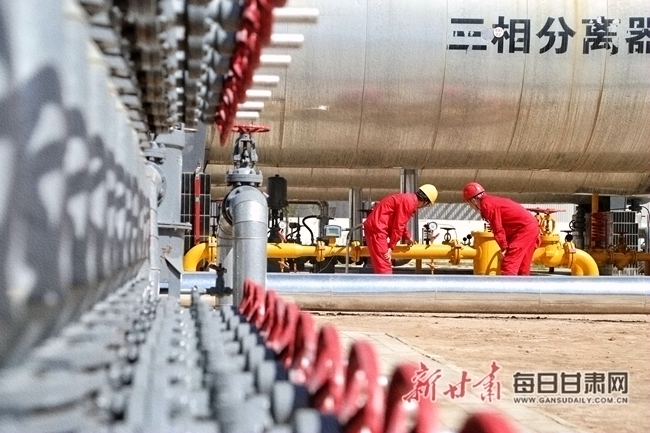
“智能运营”为员工“减员”“增技”
有效解决油田开发规模与用人成本之间的矛盾,是油田转型过程中都要面临的新课题,“目前,我们厂有120名一线员工,完全脱离传统的驻井驻站工作环境,适应了新型生产生活模式。”采油十一厂数字化与科技信息中心副主任何建军介绍道,采油作业区构建新型劳动组织架构,通过建设无人值守站点,改造中心站,结合生产、安全、工艺等需求,搭建生产组织运行平台,优化生产指挥组织方式,推动劳动组织架构改变和扁平化管理,降低劳动用工总量,提高内生动力与劳动效率,激发创新创效活力。
紧扣无人值守站建设,有效推进中心站管理模式,把员工从单井、站点撤出统一到中心站,通过“优化并转、瘦身减负”,在全厂5个作业区建成了17座中心站,盘活了内部用工500余人,实现了站点主流程、关键区域及现场作业的不间断实时监控,减少了员工出入生产现场的频次与操作频率,提升了工艺本质安全。同时,集中管理人员后,解决了员工吃、住、娱乐等涉及民生的关键问题,极大的改善了员工的生产生活条件,有效增强了员工集体荣誉感和团队凝聚力。
此外,采油十一厂积极开创互联网+培训新模式,紧贴员工培训及创新需要,积极探索技术先进性与需求贴合性的最佳结合方式,充分利用VR、AR等时下高端智能技术,通过打造虚拟微课录播互动室、安全培训体验室、工具设备拆解室、体感培训室等四室,在培训中采用VR虚拟现实技术,让员工身临其境进行站点风险辨识体验操作,通过手机APP进行设备拆解练习,将培训内容变成游戏学习,提高员工学习兴趣,改变以往培训课程的“一次性”效果,通过便捷的课程录播,实现一次录播,反复学习,培训覆盖面从“一个班”变成“所有人”。 通过互联网+创新,形成“高大上”与“接地气”的智能化工作培训体系,实现了培训、交流、创新三方面作用发挥,极大提高了员工的培训积极性。2018年以来课程培训受益人员增加31倍,实现培训率100%。解决一线问题116项,创新发明成果21项,同时减少纸张浪费,共节约培训等费用124万元。 在全面建成智慧油气田基础上,以实际作为助力能源行业高质量发展,为保障国家能源安全作出新的更大贡献。(周沛龙)
版权声明
为加强原创内容保护,日前,甘肃日报、甘肃日报报业集团各子报、甘肃新媒体集团各平台已将其所有的版权统一授予甘肃媒体版权保护中心进行保护、维权及给第三方的授权许可。即日起,上述媒体采访、拍摄、编辑、制作并刊登的,包括文字、图片、摄影、视频、音频等原创作品,文创产品、文艺作品,以及H5、海报、AR、VR、手绘、沙画、图解等新媒体产品,任何机构、媒体及自媒体未经甘肃媒体版权保护中心许可,不得转载、修改、摘编或以其他方式复制并传播上述作品。
如需使用相关内容,请致电0931-8159799。
甘肃媒体版权保护中心
相关新闻
- 2021年04月29日长庆油田采油七厂爱国主义教育基地在山城堡战役纪念园揭牌
- 2021年04月13日长庆油田采油七厂“三查三促”提升本质化安全水平
- 2021年03月17日长庆油田采油七厂上产不忘抓安全
- 2021年03月17日长庆油田采油七厂“四前”管理促安全